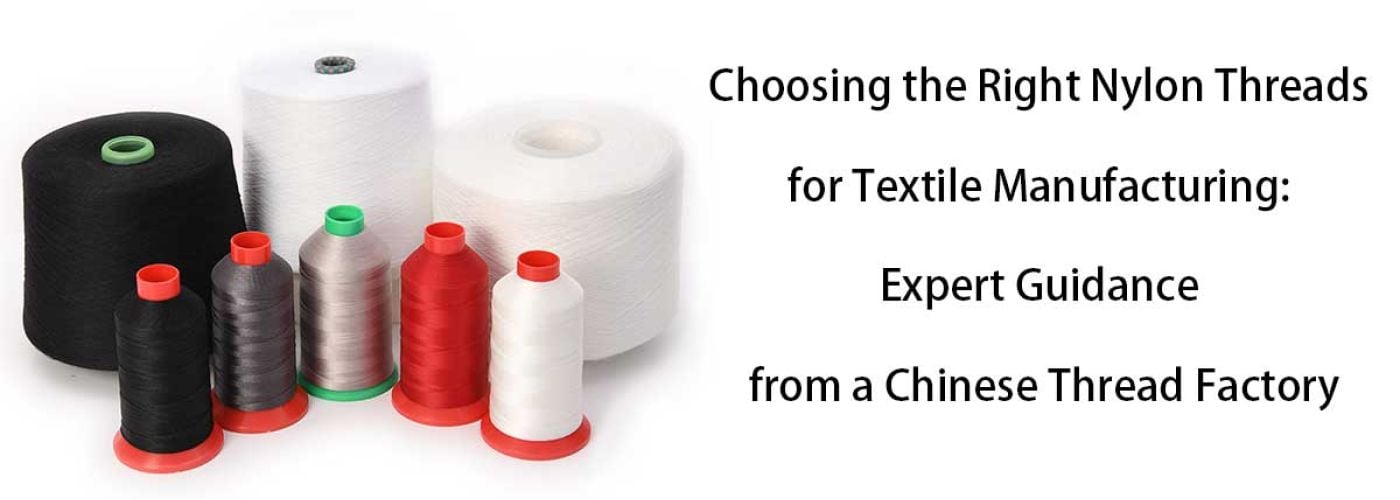
Choosing Nylon Threads for Textile Manufacturing: Expert Tips from a Chinese Factory
Selecting the appropriate thread is important for efficient, high-performing textile production. Nylon thread, in particular, remains a top choice for many manufacturers due to its strength, versatility, and resistance to wear. This guide from an established Chinese thread factory offers clear, actionable insight to help textile producers make informed decisions about bonded nylon thread selection.
Understanding Nylon Thread
What Is Nylon Thread?
Nylon thread is a synthetic filament produced from polyamide polymers. It is characterized by its high tensile strength, light weight, and inherent elasticity. These properties make nylon thread suitable for a wide range of industrial and apparel sewing applications.
Manufacturers often encounter bonded nylon thread, which features a special resin protective coating. This bond prevents the thread fibers from untwisting or fraying during high-speed sewing, supporting consistent quality and reliability on the production floor.
Key Properties of Nylon Thread
-
High tensile strength for demanding applications
-
Excellent abrasion resistance increases durability
-
Moderate elasticity allows the thread to stretch with the fabric
-
Lustrous finish for projects where appearance is key
-
Threads thickness is crucial as it affects material type compatibility, machine performance, and overall sewing quality.
MH Bonded Nylon Thread Sizes Chart
MH offers a variety of bonded nylon threads, including 210D/3, 300D/3, 420D/3, and 630D/3, among others.
Tex | Tickets Size | Denier | PLY | Averages Strength | Elongation Min-Max | Recommended Needle Size | |
(T) | (TKT) | (D) | --- | (kg) | (%) | Singer | Metric |
35 | 80 | 100D | 3 | ≥2.1 | 13-22 | 12-14 | 80-90 |
45 | 60 | 138D | 3 | ≥3.0 | 23-32 | 14-16 | 90-100 |
70 | 40 | 210D | 3 | ≥4.5 | 23-32 | 16-18 | 100-110 |
90 | 30 | 280D | 3 | ≥6.0 | 24-33 | 16-20 | 100-120 |
135 | 20 | 420D | 3 | ≥9.0 | 25-34 | 19-23 | 120-160 |
210 | 13 | 630D | 3 | ≥13.5 | 25-34 | 22-24 | 140-180 |
What Is Nylon Thread Used For?
Nylon thread plays a critical role in several sectors of the textile industry. Its unique performance characteristics enable sewing across diverse product categories. Nylon thread is also highly effective for producing various types of bags, such as backpacks, handbags, tote bags, and corn hole bags, due to its strength and durability.
Industrial Applications
-
Upholstery: The strength and abrasion resistance of bonded nylon thread make it a standard choice for stitching heavy upholstery fabric, vehicle interiors, and automotive seating.
-
Footwear and Leather Goods: Nylon thread stretches under load while maintaining seam strength, lending itself well to shoes, handbags, and luggage manufacturing.
-
Outdoor and Safety Gear: The material’s resistance to UV rays and chemicals enhances its suitability for tents, tarpaulins, harnesses, and safety equipment.
-
Holsters: The durability and distinct appearance of stitches made with nylon thread make it ideal for heavy-duty items like holsters, where choosing the right thread size is crucial for long-lasting performance.
Apparel Manufacturing
-
Sportswear and Swimwear: The elasticity and smooth finish of nylon thread are ideal for seams that require flex, such as in athletic apparel and swimwear.
-
Lingerie and Undergarments: Nylon’s fine denier options allow for delicate stitching without sacrificing strength.
-
Lightweight Thread: Specific nylon thread sizes, known as lightweight thread, are suitable for sewing delicate items such as garments, thin leather wallets, tents, and outdoor garments. This type of thread is popular for light sewing projects due to its inconspicuous stitch appearance, versatility, and compatibility with various needle sizes.
Specialty Uses
-
Decorative Stitching: The thread’s lustrous surface and array of available colors contribute to beautiful finish work in embroidery, quilting, and ornamental seams.
-
Technical Textiles: Where reliability and durability are non-negotiable, bonded nylon thread is a preferred component in industrial textiles and filtration materials.
-
Heavy Fabrics: Bonded nylon thread is ideal for sewing materials like upholstery, leather, and other heavy fabrics, including vinyl. Its strength and versatility make it suitable for handling the specific challenges presented by these materials.
How to Identify and Select Nylon Thread
For manufacturers striving for consistent, high-performance production, understanding how to identify and evaluate nylon thread is critical. The following attributes should guide your selection process:
1. Verify the Thread Composition
Always confirm the thread material is 100% nylon. Reputable suppliers, like established Chinese thread factories, provide technical datasheets outlining material composition and performance metrics.
2. Understand Bonded Nylon Thread Benefits
Bonded nylon includes a protective resin. This bond:
-
Minimizes fraying
-
Prevents thread splitting at needle penetration points
-
Reduces downtime and increases productivity on high-speed machines
It is favored for industrial applications requiring robust, uniform seams.
3. Consider Thread Size and Denier
The thread size determines stitch appearance and seam strength. Heavier fabrics and stress-bearing seams call for thicker thread. Common size identifiers include Tex, Denier, or ticket numbers.
-
Tex: Measurement of thread mass per 1,000 meters. Higher Tex = thicker thread.
-
Denier: Mass in grams per 9,000 meters. Common for filament threads.
-
Ticket Number: Often used in Europe and Asia; lower numbers indicate thicker threads.
Example: Upholstery requires Tex 70–135 (approx. Denier 700–1300), while fine lingerie may use Tex 30–40.
When selecting thread, consider the recommended thread sizes based on material type, machine compatibility, and desired stitch appearance.
4. Assess Abrasion Resistance
Abrasion resistance is a defining benefit of nylon. Bonded nylon thread should show minimal wear when tested against fabric surfaces or during repeated machine passes. For high-traffic items such as workwear or gear, this property is essential.
5. Evaluate Stretch and Elasticity
"Nylon thread stretches" modestly under tension, accommodating flexible or elastic textiles without thread breakage. This elasticity supports both form-fitting apparel and technical textiles subject to movement.
6. Match Needle Size to Thread
High-speed production benefits from proper needle size selection, especially for machine sewing. Incorrect pairing can cause thread breaks or skipped stitches. Suppliers will recommend appropriate needle sizes for each thread thickness (e.g., Tex 70 thread pairs with needle sizes 110/18–120/19).
7. Verify Colorfastness and Finish
Superior quality nylon thread from leading Chinese factories resists fading and maintains luster after repeated machine washes or sunlight exposure. Review colorfastness scores in supplier documentation for assurance.
8. Ask About Production Standards
Trust suppliers that adhere to ISO certifications or equivalent quality management processes. These benchmarks ensure consistent thread diameter, tensile strength, and bonding quality in every shipment.
Choosing the Right Nylon Thread Supplier
Partnering with an experienced Chinese thread factory ensures access to a broad assortment of bonded nylon threads, reliable quality control, and technical support. Top manufacturers stand out through:
-
Comprehensive product ranges bridging various sizes, colors, and finishes
-
Detailed technical documentation for each product
-
Dedicated support teams to address questions about thread size, abrasion resistance, and application fit
-
Transparent sourcing and production processes to support sustainable manufacturing goals
Selecting Nylon Thread for Manufacturing Excellence
The right nylon thread elevates textile performance, durability, and finished product quality. Key decision factors include the required seam strength, material characteristics, thread size, and specific application. It is also easier to find specific types of thread, such as right-twist polyester thread, which can be more readily available compared to other variations.
Manufacturers are encouraged to collaborate closely with reputable thread factories to evaluate bonded nylon thread options, including technical samples and in-depth product guidance. This ensures optimal compatibility with fabrics, machinery, and end-use requirements.
For textile producers intent on maximizing reliability and output, comprehensive thread assessment is not optional. It is foundational for long-term operational success.